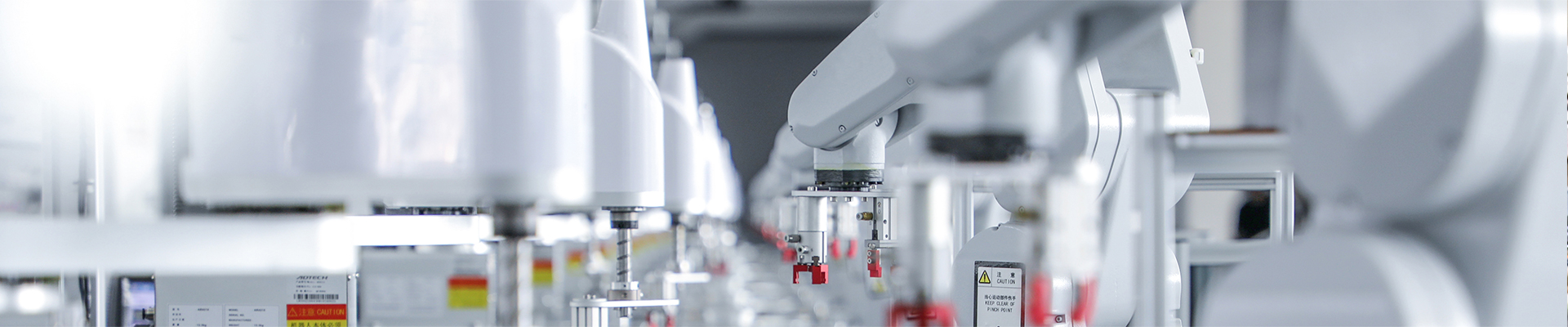
Quality
Get the latest price? We'll respond as soon as possible(within 12 hours)
Quality management - An integral part of who we are
When designing and manufacturing ac motor and dc motor, nema motor, brushless motor controllers, effective quality management of the entire process is critical to ensuring successful outcomes.We use an integrated quality management system, certified to ISO9001 standards as well as industry standard approaches such as Lean 6 Sigma and 5S to ensure the best quality output from both the design and manufacturing sides of the business.
We believe in a culture of continuous improvement and train all new staff in the importance of quality management to the business, as well as the key areas they can help us to improve. We encourage openness and fairness in dealing with issues where they arise to ensure that all staff feel empowered to discuss any potential improvements, issues or concerns they may have.We continuously measure and analyse our processes to improve efficiency and output, reducing waste and adding value in the process.
Our aim is to deliver value for money to all of our customers by learning from and incorporating industry best practice in all areas of the business.
A flexible approach to new developments
The quality management process starts with the specification.
If you’re interested in developing either a modified stock motor controller or a custom designed motor controller, then we will work closely with you to develop a detailed specification that you are happy with. Depending on the nature of the specification it may be a requirement that certain feasibility studies are required to ascertain whether a potential solution is viable or not. Where this is the case we may apply a hybrid, staged project management approach in order to quickly prototype and explore potential new ideas whilst at the same time controlling cost and time constraints.
We understand that quality management is not just about process controls and external certifications, but also about culture and approach. We adopt a flexible strategy, coupled with a commitment to reviewing our work and customer feedback to learn from our mistakes. Where mistakes or inefficiencies occur, we employ DMAIC and RCA models to accurately identify causes and drive them out of the process.
We continuously invest in new data gathering and analytics tools to ensure that we have accurate reporting on all areas of the business, enabling management to make quick, key decisions in an informed and sensible manner. On top of this we maintain up to date contingency and risk management planning across all areas of the business to reduce the potential impact of any external disruption. Whether it be component supply issues, political changes or other issues, we work hard to mitigate these to ensure we can continue to deliver value for money to our customers.
Quality Leads to Value
We understand that you don’t want to pay for inefficiencies in our factory or delays in shipments.
You want to pay a fair price for well produce goods, delivered on time. That’s why we take a highly proactive approach to quality management.
We understand that quality management is the key to delivering value to our customers through improved processes and data driven continuous improvement.